Utah Tech University's Art Department Chair Created a Giant 3D Printed Dinosaur with QIDI 3D Printers
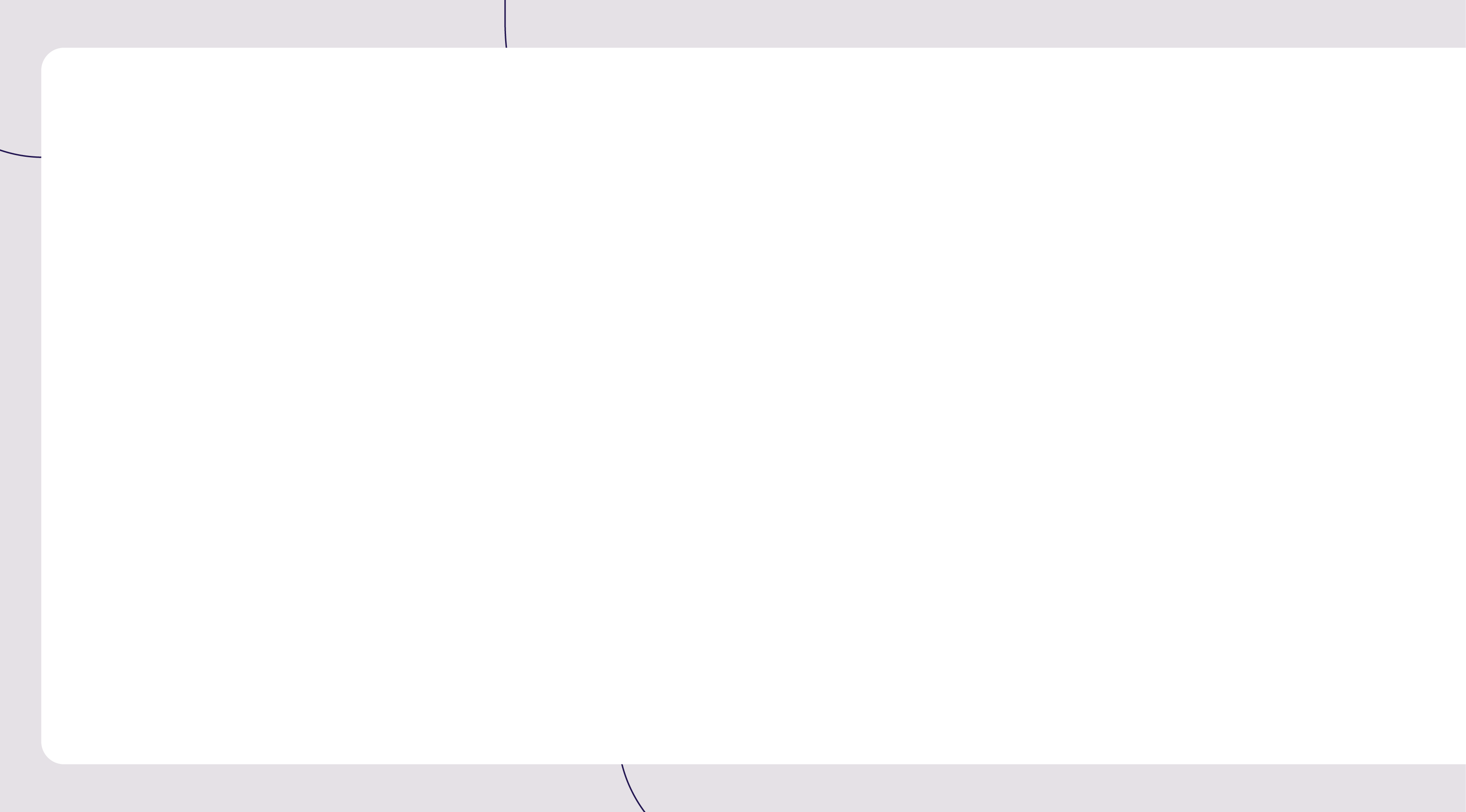

Shoppers at the Red Cliffs Mall in St. George, Utah, are getting an unexpected prehistoric surprise: a massive, 39-foot-long Tyrannosaurus rex skeleton. But this T. rex isn't ancient history; it's a modern marvel, 3D printed by Alex Chamberlain, the Art Department Chair at Utah Tech University. Using QIDI's X-Max 3 and X-Plus 3D printers, Chamberlain brought this giant dinosaur replica to the St. George community. It's a stunning example of what 3D printing can do and a cool educational piece for everyone visiting the mall. Here's the story of how this incredible project came together.

How the T. rex Project Began
Alex Chamberlain's inspiration wasn't exactly new – he's always been fascinated by dinosaurs. He told St. George News about a key moment visiting a cast of a T. rex skull in Provo, Utah: "I've always been a dinosaur nut, but that experience of walking up to that skull, and having it chest level and being able to sort of compare my size was really transformative for me. It really inspired me to want to share that experience with others."
That encounter sparked the idea to build a full-scale T. rex. As an animation professor, Chamberlain saw a way to blend his teaching skills with his love for paleontology. He knew that complete T. rex skeletons are rare (only about 30 exist worldwide) and that casts cost a fortune—around $120,000—putting them out of reach for many places. Frustrated by this, Chamberlain turned to his skills in digital modeling and 3D printing to create an accurate, affordable version. The T. rex was the perfect pick: everyone knows it, and its sheer size is guaranteed to impress mall-goers of all ages.

Why 3D Printing Was the Perfect Choice for This Project
Traditional museum displays of dinosaur skeletons require extensive resources and specialized facilities. 3D printing technology offered Chamberlain a revolutionary alternative to bring his vision to life.
Much Lower Production Costs Than Traditional Casting
Museum-quality replicas usually involve pricey casting methods. As mentioned, getting a T. rex cast commercially costs about $120,000 – way too expensive for many. 3D printing slashed these costs because there's no need for molds, and it wastes less material. This made a project that seemed financially impossible suddenly doable.
Precise Bone-by-Bone Digital Customization
3D printing gave Chamberlain amazing control. Working with digital models, he could adjust the size, fix anatomical details, and double-check accuracy before printing anything. This meant he could easily make changes during the design phase, something much harder with traditional methods.
Component-Based Assembly for a 39-Foot Giant
Maybe the biggest plus for such a huge project was printing the skeleton in sections. Each bone could be printed separately and then put together. This solved a lot of practical problems: it was easier to transport manageable pieces to the mall, the parts could be sized to fit the QIDI 3d printers, individual pieces could be reprinted if needed, and assembly at the mall was simpler. This piece-by-piece approach was key to turning a digital design into the giant skeleton now wowing visitors at Red Cliffs Mall.
The Tools Behind the T. rex: QIDI's X-Max 3 and X-Plus Printers
To pull off this dinosaur-sized project, Chamberlain relied on two QIDI 3d printer models: the X-Max 3 and the X-Plus. They worked well together for the job.

Large Build Volumes for Printing Substantial Bone Segments
Both the QIDI X-Max 3 and X-Plus feature spacious build platforms, allowing Chamberlain to print sizeable bone components in single runs. This capability significantly reduced the number of separate pieces needed for the 39-foot skeleton, simplifying the assembly process while maintaining structural integrity.
Enclosed Printing Chambers for Consistent Quality
The enclosed design of both printer models provided a controlled printing environment—essential for maintaining consistent temperature during the extended print sessions required for larger components. This feature helped prevent common 3D printing issues like warping or layer separation that can occur with temperature fluctuations.
Reliable Performance for Extended Print Durations
Creating a project of this magnitude required hundreds of hours of continuous printing. The QIDI printers demonstrated exceptional reliability throughout this demanding process. Each bone segment, from the massive femurs to the delicate tail vertebrae, required precise extrusion over extended periods—a testament to the machines' durability.
Dual-Machine Workflow for Increased Productivity
Using both the X-Max 3 and X-Plus in tandem allowed Chamberlain to significantly accelerate the production process. While one printer worked on larger structural components, the other could simultaneously produce elements with multiple smaller parts. This parallel workflow was crucial for completing such an extensive project within a practical timeframe.

The Labor of Creation: Piecing Together a Prehistoric Puzzle
Getting from digital files to a giant skeleton took careful planning and a lot of work. First came the 3D models of the T. rex bones. These digital files were fed into slicing software, which tells the printer how to build the object layer by layer. With so many bones to print, just getting the files ready was a big job.
Then, the QIDI printers started the long process of printing, layer by layer, slowly forming each bone out of filament. Choosing the right material was also key – it needed to be strong but not too heavy or expensive. Chamberlain used ABS plastic for its strength and ability to be solvent-welded together with acetone. Once all the pieces were printed, the real puzzle began: carefully assembling each bone segment, making sure everything lined up correctly to create the final, impressive skeleton.
39-Foot 3D Printed T. rex Now on Display at Red Cliffs Mall
The finished T. rex skeleton is now a major attraction at the Red Cliffs Mall in St. George, grabbing the attention of shoppers and visitors.

A Life-Sized Prehistoric Giant
The skeletal display stretches an impressive 39 feet in length and stands 13 feet tall at the hip. If positioned fully upright, this prehistoric giant would tower at approximately 20 feet tall. These true-to-life dimensions give visitors a genuine sense of the T. rex's imposing presence, something that's difficult to appreciate from textbooks or smaller museum models.
Community Engagement Through Interactive Events
The mall has embraced the dinosaur as more than just a display, organizing a "Name the Dino" contest where community members can give the T. rex its official title. This contest is being held online through the mall's website and social media channels.
As part of the T. rex event, Red Cliffs Mall is giving away various prizes, including season passes to Jellystone Water Park, $100 gift cards, and passes to the nearby dinosaur museum. These incentives have helped generate significant local interest in the exhibit.
Educational Partnership with Local Attractions
Mall General Manager Cory Ashby explained that the installation perfectly fits the mall's goal of bringing people together and engaging the community. The mall has partnered with local dinosaur attractions, including the nearby dinosaur museum, and is launching a "Passport to Summer" program designed to get kids outside and engaged in fun activities.
This collaboration transforms the mall from a simple shopping destination into a community hub for education and entertainment, with the 3D printed T. rex serving as the perfect prehistoric ambassador.

Build Your Spectacular 3D Printed Project with QIDI
Alex Chamberlain's T. rex project is a fantastic example of creativity meeting technology. Using QIDI X-Max 3 and X-Plus printers, he turned a digital concept into a massive, 39-foot dinosaur that's now a hit with the St. George community.
It shows how 3D printing is opening doors for educators, artists, and makers, making ambitious projects like this more achievable than ever before. Whether it's for education, art, or invention, the right tools can help bring big ideas to life.