What 3D Printer Can Make Shoes?
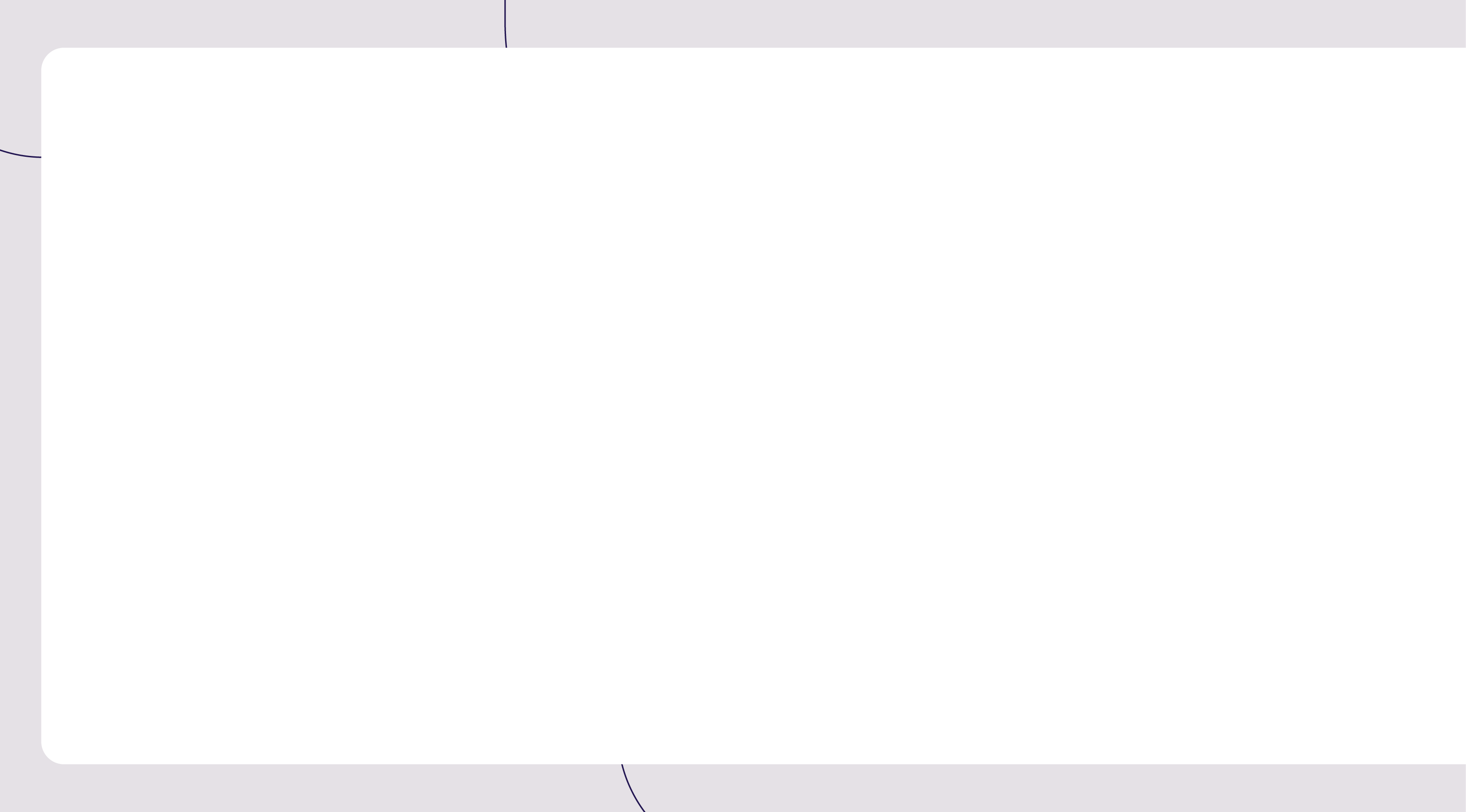
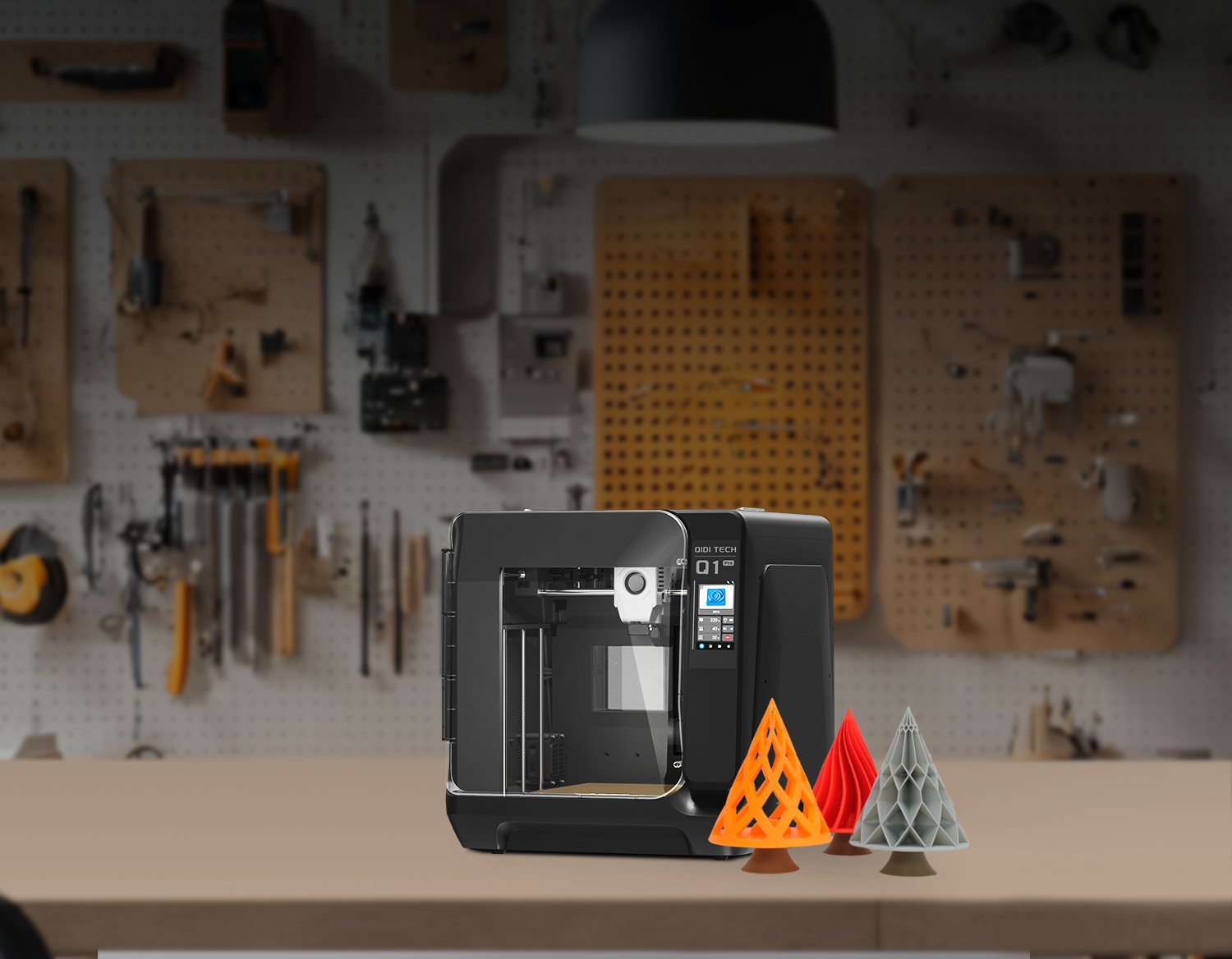
3D printing now offers a practical way to create custom footwear, designed for individual fit and style. While it's an exciting prospect, it raises a key question: can just any 3D printer do the job, or are special features and materials needed to create wearable shoes from a digital file? The short answer is yes, many 3D printers can make shoes. However, success largely depends on the printer's capabilities, the materials you use, and the shoe design itself. This guide will cover the important printer features, suitable printer types, and other key considerations for printing your own shoes.
TPU/TPE: Why 3D Printed Shoes Need Them & Their Printing Challenges

If you want to 3D print shoes that are actually comfortable and practical to wear, the first major challenge you'll face is working with flexible materials. Without flexibility, a shoe can't move naturally with your foot or absorb impact effectively, making it more of a rigid display piece than usable footwear.
The most suitable materials for achieving this needed flexibility are Thermoplastic Polyurethane (TPU) and Thermoplastic Elastomer (TPE). They offer excellent elasticity and durability, which are ideal for shoes. However, it's precisely this flexibility that makes them difficult to 3D print. Common issues include the filament bunching up and jamming the extruder, thin strands of plastic (or "stringing") appearing where they shouldn't, and layers not sticking together strongly enough.
Types of 3D Printers and Their Suitability for Shoes
If flexible materials are key for shoes but can be tricky to print, which 3D printing technologies actually work well for making footwear?

FDM / FFF
This technology, which builds objects by extruding melted plastic filament layer by layer, is the most widespread and practical choice for most individuals and small businesses.
Advantages: There's a good variety of flexible filaments like TPU available. FDM 3D printers are usually more affordable than other types, and there's a large online community for support and advice.
Disadvantages: As discussed, printing flexible filaments well requires specific printer features. Also, the layer lines common to FDM prints will be visible, which may or may not be an issue depending on what you want the shoe to look like.
SLA / Resin Printers
SLA printers use a UV light source (a laser or projector) to harden liquid resin layer by layer, creating objects with very fine details.
Advantages: SLA is excellent for producing parts with very smooth surfaces and complex details, much more so than typical FDM prints. Flexible resins are available, which makes printing shoe components possible.
Disadvantages: Flexible resins are less common and more expensive than FDM filaments. These resins typically offer lower durability for everyday shoe use compared to TPU. Safety concerns include toxicity of uncured resin (requiring careful handling and thorough post-processing) and potential skin contact issues even after curing. Most consumer SLA printers also have smaller build volumes than FDM machines, limiting shoe size or requiring multi-part designs. These factors make SLA less suitable for fully wearable, everyday footwear.
SLS
SLS technology uses a powerful laser to fuse powdered materials, such as nylon or TPU powders, together.
Advantages: SLS can create very strong, durable, and complex parts. Because the surrounding unsintered powder supports the object during printing, no separate support structures are needed. This makes it a great choice for professional-quality 3D printed footwear, capable of handling complex designs.
Disadvantages: The main drawback is the extremely high cost of SLS machines and their materials, which puts them out of reach for hobbyists and most small businesses.
MJF and Other Powder Bed Fusion Technologies
Technologies like HP's Multi Jet Fusion are similar to SLS, also using powdered materials. They offer similar capabilities in terms of part strength and complexity, using materials like TPU. These are industrial systems used by large footwear companies for prototypes and sometimes small production runs, but they share the same high cost as SLS.
FDM Printer Require Specific Features for Shoemaking
Among these types of 3D printers, FDM is particularly popular for shoemaking due to its accessibility. However, its success with flexible filaments hinges on specific features, making some critical for good results.
- Direct Drive Extruder: Provides better control for soft, flexible filaments like TPU, reducing jams and improving print precision for shoe components.
- Constrained Filament Path: A fully enclosed path from drive gear to nozzle prevents flexible TPU from kinking or escaping, crucial for reliable shoe prints.
- All-Metal Hotend: Handles higher TPU printing temperatures without PTFE tube degradation, ensuring safer, consistent melting for durable shoe parts.
- Sufficient Build Volume: Shoes require a large print area. A minimum of 200x200x200mm (approx. 8x8x8 inches) is typically needed to print a shoe or its largest parts. Printing in sections can allow for smaller areas.
- Heated Print Bed: Vital for TPU, ensuring the first layer sticks well and preventing warping on large shoe bases. Use PEI sheets or similar surfaces for good grip.
- Reliable Extrusion & Temperature Control: Key for shoe strength. Consistent material extrusion and stable hotend/bed temperatures ensure strong layer bonds.
- Controllable Part Cooling Fan: Important because TPU often needs less cooling than PLA. Adjustable fan speed (via slicer software) is needed to prevent weak TPU layer adhesion.
- Sturdy Frame & Mechanics: Essential for large shoe prints. A rigid frame prevents wobble and vibration, ensuring smoother, more accurate printing for better quality footwear.
These features are essential for an FDM printer to successfully create footwear, especially with flexible materials.

More Than Just the Printer: Other Important Factors
Having the right 3D printer is a big step, but other elements are also crucial for successfully printing wearable shoes.
- Filament Quality: The quality of your TPU/TPE filament significantly impacts the outcome. Opt for high-quality material from reputable brands. Cheaper flexibles can cause printing issues and poor shoe quality due to inconsistent diameters, moisture absorption, or inferior material properties.
- Slicer Settings: Slicer software, which prepares your 3D model for printing, needs careful tuning for flexibles. Settings like print speed (usually slower), temperature, retraction (for stringing), infill, and cooling fan speeds require testing to suit your specific filament and shoe design.
- Shoe Design: The shoe's design itself is crucial and must be optimized for 3D printing. Considerations include minimizing overhangs to reduce difficult-to-remove supports on flexible prints, build plate orientation for strength, and choosing between single-piece or multi-part assembly. The shoe's intended use also influences these choices.
- User Skill and Patience: Printing complex items like shoes with flexibles requires practice and experimentation. Expect issues like stringing or bed adhesion problems; troubleshooting is part of learning. Patience and a systematic approach to adjusting settings are essential for success.
While a good printer provides the essential foundation, these other elements truly dictate the journey and the final success of any 3D printed shoe. Overlooking any of them can significantly hinder your results.
Level Up With the Right 3D Shoe Printer!
Creating your own 3D printed shoes combines technology with personal creativity. While FDM printers that have features like direct drive extruders, adequate build volumes, and heated beds are the most practical way to start, your success will also depend on using good materials, carefully tuning your printer settings, and having a well-thought-out design. It's a process that often requires some trial and error, but it offers exciting opportunities to make footwear that is truly your own.